Roping in the years at Doblar Arena
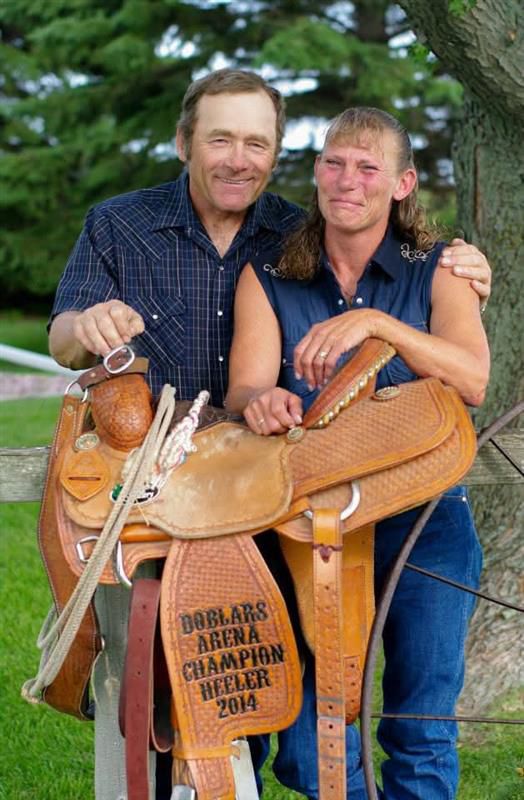
By Jen Burris
For over three decades, John and Dian Doblar have hosted team roping competitions at their home in Lake County, South Dakota.
“We’ve been putting on team ropings at our house for probably 37 or 38 years,” Dian Doblar said.
Team ropers work together to catch a horse, with one roping the head of the horse, and one roping the heels.
The arena they built for it was first made of railroad ties and golden wire, but it now has sucker rod around the whole thing. There’s an audience section to watch and a sandbox area for kids to play in, and a concession stand for snacks and beverages.
John works to get sponsors for the competition to increase winnings for participants.
When John isn’t hosting and roping at home, he travels around to compete in other roping competitions, in towns such as New Underwood, Aberdeen, Sisseton, Flandreau, and Sioux Falls.
But it’s not just the couple running the show, it’s a family affair, their four adult children, 10 grandchildren, and one great-grandchild help too.
Dian and her son, Alan often push the cattle, while her grandson, Tristan, usually takes the ropes off at the other end. Two of her three daughters, Jill and Nikki, run the office, and Jill’s youngest boy runs the concession stand.
“It’s pretty fun,” Dian said. “They’re all working and we usually either go out for supper afterwards or bring stuff in to feed them all.”
Each summer they host seven team roping competitions. Participation has grown over the years through word of mouth, flyers, and social media. Doblar’s Arena often promotes their competitions on the Sioux Empire Team Roping Facebook group. Now the competitions frequently bring about 100 teams.
The competitions are usually held on Sundays. “There are other people who host on Saturdays, so we try to hit the days they’re not going elsewhere,” she said.
It can be quite the endeavor to organize these events, but Dian finds that after the first one of the season the family has everything situated and they settle into a routine.
The family time is Dian’s favorite part of hosting the competitions. “I get to see them all, and they all get into it.”
Alan enjoys roping too, and a couple of the grandchildren are interested in learning how to rope as well.
While Dian acknowledges that her children and grandchildren were forced into the hosting and roping life, they grew to like it.
Alan will likely take over the operation sometime in the future, but in the meantime, John is ready and willing to talk to people interested in learning more about roping.
For more information visit Doblar’s Arena Facebook group. Their next competition is the 38th Annual Draw Pot Team Roping and Saddle Roping competition on Saturday, Aug. 23 at 1 p.m. For those who would like to participate, pre-registration is required. For more information or to enter, call John at 605-270-1458.
For over three decades, John and Dian Doblar have hosted team roping competitions at their home in Lake County, South Dakota.
“We’ve been putting on team ropings at our house for probably 37 or 38 years,” Dian Doblar said.
Team ropers work together to catch a horse, with one roping the head of the horse, and one roping the heels.
The arena they built for it was first made of railroad ties and golden wire, but it now has sucker rod around the whole thing. There’s an audience section to watch and a sandbox area for kids to play in, and a concession stand for snacks and beverages.
John works to get sponsors for the competition to increase winnings for participants.
When John isn’t hosting and roping at home, he travels around to compete in other roping competitions, in towns such as New Underwood, Aberdeen, Sisseton, Flandreau, and Sioux Falls.
But it’s not just the couple running the show, it’s a family affair, their four adult children, 10 grandchildren, and one great-grandchild help too.
Dian and her son, Alan often push the cattle, while her grandson, Tristan, usually takes the ropes off at the other end. Two of her three daughters, Jill and Nikki, run the office, and Jill’s youngest boy runs the concession stand.
“It’s pretty fun,” Dian said. “They’re all working and we usually either go out for supper afterwards or bring stuff in to feed them all.”
Each summer they host seven team roping competitions. Participation has grown over the years through word of mouth, flyers, and social media. Doblar’s Arena often promotes their competitions on the Sioux Empire Team Roping Facebook group. Now the competitions frequently bring about 100 teams.
The competitions are usually held on Sundays. “There are other people who host on Saturdays, so we try to hit the days they’re not going elsewhere,” she said.
It can be quite the endeavor to organize these events, but Dian finds that after the first one of the season the family has everything situated and they settle into a routine.
The family time is Dian’s favorite part of hosting the competitions. “I get to see them all, and they all get into it.”
Alan enjoys roping too, and a couple of the grandchildren are interested in learning how to rope as well.
While Dian acknowledges that her children and grandchildren were forced into the hosting and roping life, they grew to like it.
Alan will likely take over the operation sometime in the future, but in the meantime, John is ready and willing to talk to people interested in learning more about roping.
For more information visit Doblar’s Arena Facebook group. Their next competition is the 38th Annual Draw Pot Team Roping and Saddle Roping competition on Saturday, Aug. 23 at 1 p.m. For those who would like to participate, pre-registration is required. For more information or to enter, call John at 605-270-1458.